Location: Buffalo, New York, United States I Email: [email protected] I Call us: +1 (716) 472-2893 I WhatsApp: +1 (716) 472-2893
SCREENING MEDIA
Our high carbon woven wire cloth is renowned for its exceptional durability, precision, and resistance to impact, establishing trust among clients worldwide for more than 35 years.
Screening Media
Elevate your screening process to new heights with our diverse selection of screens designed for precision sizing and built to last. Our offerings include top-notch high carbon steel, 304, 316, and 430 Stainless Steel, polyurethane screens, and abrasion resistance perforated plates (HARDOX).
Our screens are manufactured with the highest quality materials, hardness, ductility, tensile strength and durometer. Only a few manufacturers use state-of-the-art equipment and manufacturing tolerances to assure the longest lasting screens on the market. We manufacture replacement screens that fit equipment the following OEMs: Deister, Terex, etc.
No matter if you’re working with a horizontal, inclined, or trommel screen, we guarantee we can provide you with the ideal solution to boost your operational efficiencies. You can place your trust in our products to fulfill your precise screening requirements and enhance performance while simultaneously reducing your cost per ton produced.
They are often used for precise screening in general applications. Our high carbon woven wire cloth has been renowned around the world for its exceptional durability, precision, and resistance to impact for more than 35 years.
Our commitment to quality is evident through our adherence to EU, GB, and ASTM standards. Our woven wire cloth has been widely accepted by clients from North America, Australia, Europe, and the Middle East for its high durability, precision, and impact resistance.
Commonly used where there is impact and heavy-material applications because it absorbs impact better than other applications. Can take up to 3-4 times more impact than single wire screens, making it an affordable alternative to perforated plate. It also provides up to 50% more open area than plate, making it a great choice for when more productivity and impact resistance is needed.
The double wire screen features pre-undulated wires with precise spacing. It offers a high screening surface percentage, ensuring accurate classification of materials that are less prone to blockage, in addition toexcellent vibration resistance and durability.
001![]() | 002![]() | 003![]() |
004![]() | 005![]() | 006![]() |
007![]() | 008![]() | 009![]() |
Used when precise screening is not needed and with materials that have a high degree of humidity and plasticity because they offer more open area than a traditional square mesh. They are commonly used to remove fines from stone crush and provide more open area than square mesh. They can only be used with cubic material or when precise screening is NOT needed.
Our screens are manufactured with the highest quality standards of wire hardness, ductility, and tensile strength. Only a few manufacturers use state-of-the-art weaving equipment for tight crimps, weaves, and manufacturing tolerances in order to assure the longest lasting screens on the market.
Some materials tend to adhere to the screen or get stuck on it due to their humidity, plasticity or shape, which reduces the production capacity of the screen and increases the downtime of the machine. A self-cleaning screen not only prevents pegging and binding, but it also produces more product and makes the screen last longer.
The wires of a self-cleaning screen vibrate independently from each other - they are not woven. The engineered design allows each wire to vibrate independently from each other, increasing the vibration of the material and helping with its stratification.
Effective stratification of the material eliminates fines faster and, therefore, reduces build-up on the screen.
A self-cleaning screen has a higher percentage of screening surface (compared with a traditional square opening screen), which makes them highly recommendable for improving production capacity. Our high carbon woven wire cloth is renowned for its exceptional durability, precision, and resistance to impact resistance. For extremely sticky materials, stainless steel wire is recommended.
Start decreasing the cost per ton of your precise screening and/or fine elimination processes!
001 | 002 |
003 | 004![]() |
When it comes to oil drilling, shaker screens are a vital part of the process. Drilling rigs use shaker screens to filter out solid particles and debris, allowing only the oil to pass through. Selecting the right shaker screen is crucial to the success of any oil drilling operation. Shale shaker screens are available for the main brands like MI Swaco Derrick, Kemtron, Brandt, NOV, VSM, and FSI. Choosing the right screen for your drilling operation is essential, and these seven brands are some of the most trusted names in the industry. From MI Swaco to FSI, you can count on these brands to perform reliably and have long-lasting durability.
We carry replacement screens for most shale shakers.
Enhance your screening efficiency with perforated plates, which offer superior wear and impact resistance compared to traditional woven wire. These plates can be easily hooked or bolted onto your screener or configured as modular panels, providing versatility in installation. The openings can be customized to your preference, whether rounded, hexagonal, square or any other shape.
Choose from a variety of materials such as Abrasion-Resistant plate, Hardox, High Manganese, and stainless steel 303 and 316.
While perforated plates excel when it comes to wear resistance, it's essential to note that they may reduce the open area available for sifting compared to wire screens. However, the trade-off in open area is compensated by the increased durability and impact resistance offered by perforated plates, making them a robust choice for your scalping needs.
Polyurethane screens are a reliable alternative to high carbon steel screens in specific applications, finding their niche in coal, iron ore, copper, gold, and other ore grading, screening, and dewatering processes.
Renowned for their extended lifespan, these screens outperform their wire mesh counterparts, often lasting 8-10 times longer, contingent upon the application.
The superiority of polyurethane screens becomes evident in their heightened abrasion resistance and superior ability to withstand rubbing and scalping during production, surpassing the capabilities of metal screens. Notably, if your screener currently employs hooked metal panels, no modifications are required for a seamless transition to polyurethane screens.
These polyurethane screens exhibit full compatibility with all hook screen decks, accommodating varying crown bar sizes and locations without any issues. The tapered apertures incorporated into their design serve to eliminate near-size pegging, ensuring a smoother and more efficient screening process. Elevate your screening experience with the durability, adaptability, and enhanced performance offered by polyurethane screens.
Polyurethane panels serve as a versatile replacement for wire screens in specific applications, and at DaVinci and Tesla, we proudly offer a comprehensive range of panels and accessories designed to meet your diverse screening needs. The advantages of our urethane modular panels are numerous, including:
Extended Lifespan: last up to 8-10 times longer than steel in select applications. Urethane panels excel in extremely abrasive conditions, whether in dry or wet environments, and provide heightened durability and superior elasticity against impact abrasion. This extended lifespan translates to a significant reduction in your cost per ton produced.
Modular Replacement: our panels offer the flexibility of replacing only a small worn area, minimizing downtime and costs. For instance, a small 1x1ft urethane panel can be replaced instead of an entire 6x4ft wire panel.
Noise Reduction: enjoy a quieter screening environment with the inherent noise reduction capabilities of urethane panels.
However, it's important to note that urethane panels may have a reduced open area compared to high carbon steel screens, representing a trade-off in some scenarios.
Rest assured, DaVinci and Tesla urethane panels are designed for compatibility with a wide range of OEM panels, ensuring seamless integration into your existing screening setup. Upgrade your screening experience with the durability, efficiency, and adaptability of our urethane panels.
OEM Fastening system
Polydeck: Pin and Sleeve, Pin ang Leg, Polysnap, PolyRail Frame system
Tema Isenmann: WS85
Metso: Trellex 300LS, Trellex 305LS, Trellex 300TS
McLanahan: Classic style (u channel wide)
Linatex: Snap Deck Classic (u channel narrow), Snap Deck 2000.
Traditional urethane and rubber panels have the advantage of 8-10 times more life than a screen, BUT, their open area is significantly lower than wire mesh.
Davinci and Tesla SELF-CLEANING, HIGH VIBRATION PANELS are a better choice than traditional polyurethane panels because they offer up to 98% more open area than traditional urethane panelswithout greatly compromising their wear life. In contrast to woven metal screens AND polyurethane panels, the wires of our self-cleaning design vibrate independently, ensuring a dynamic and efficient screening process that provides more vibration to the material, creating a more efficient stratification and more efficient screening, which greatly reduces binding and pegging.
Start reducing your cost per ton now!
Dewatering Screens: Designed to recover water from wet screening processes, these screens reduce water content and remove fines, clays, and fillers from the material feed. They excel in wet applications and have high wear resistance. Trommel screen panels can be manufactured in wire mesh, urethane or a hybrid.
Molded around a tough wireframe network, Rhino Hyde Trommel Screens have been proven to outlast ordinary metal screens by up to 8x, reducing downtime and maintenance costs.
DOWNLOAD BROCHURE
SCREENING MEDIA
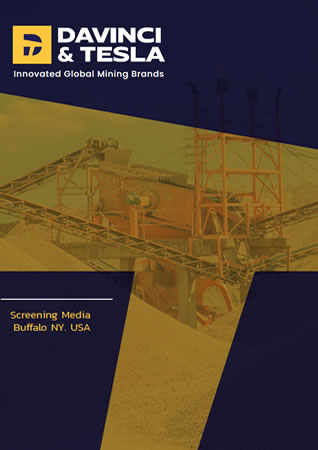
We Are Your Best Choice
Your trusted broker for equipment and mining supplies, which in the past were exclusive to OEM and distributors.
With 35 years of combined experience, we deliver unmatched expertise and service tailored to reduce unnecessary costs in your supply chain.